


Hence, there is a significant interest in developing additive manufacturing (AM) technologies that can repair the single crystal turbine blades. Additionally, if the components suffer from material loss due to prolonged service or manufacturing defects, the traditional manufacturing methods cannot restore the parent metallurgy at the damage locations. For example, a set of 40 single crystal turbine blades costs above USD 600,000 and requires 60–90 weeks for production. Due to the complex production process involving several prototyping iterations, the blade castings have a significant cost associated with them.
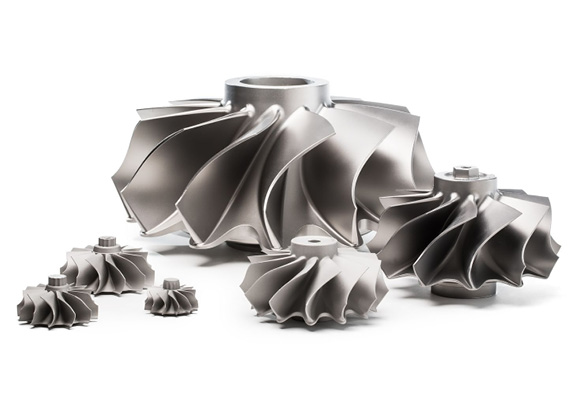
Single crystal casting is exotic as several steps of the casting process are traditionally hands-on. The turbine blades are typically fabricated using investment casting, and depending on the casting complexity, they generally display one of the three common microstructures (i.e., equiaxed or polycrystalline, directionally solidified, and single crystal). The blades are at the heart of the turbine section as they extract energy from the hot gases to generate work. The turbine section of aircraft engines (both commercial and military) is an example of one of the most hostile environments as the components in this section typically operate at upwards of 1650 ☌ in the presence of corrosive and oxidative gases.
